The Revere Ware of legend, that produced between 1939 and 1968 made a lot of fans. It was well made, really useful stuff, and iconic. Along with all that, Revere Ware the company stood behind their products, not only with a then lifetime warranty, but with a large stock of replacement parts. Take a look at this catalog of replacement parts from 1967.
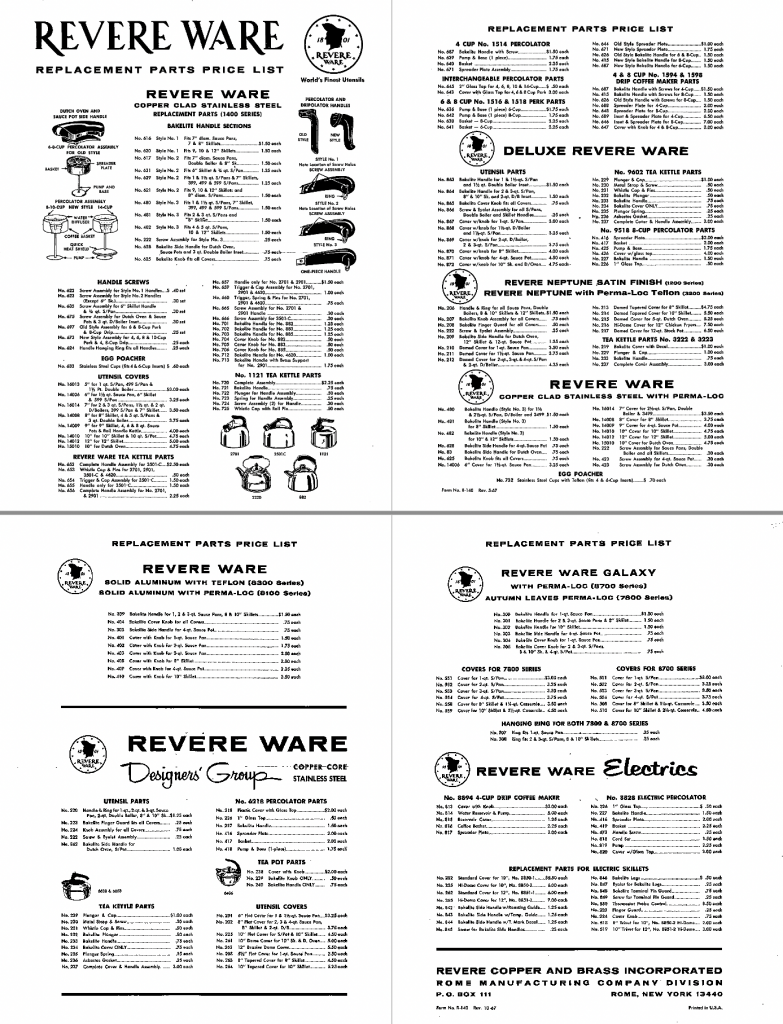
They sold everything, and I mean everything. In 1967, they sold handles for pots that hadn’t produced since 1946, lids for every style, screws, you name it. In contrast, here is a similar replacement parts catalog from 1988.
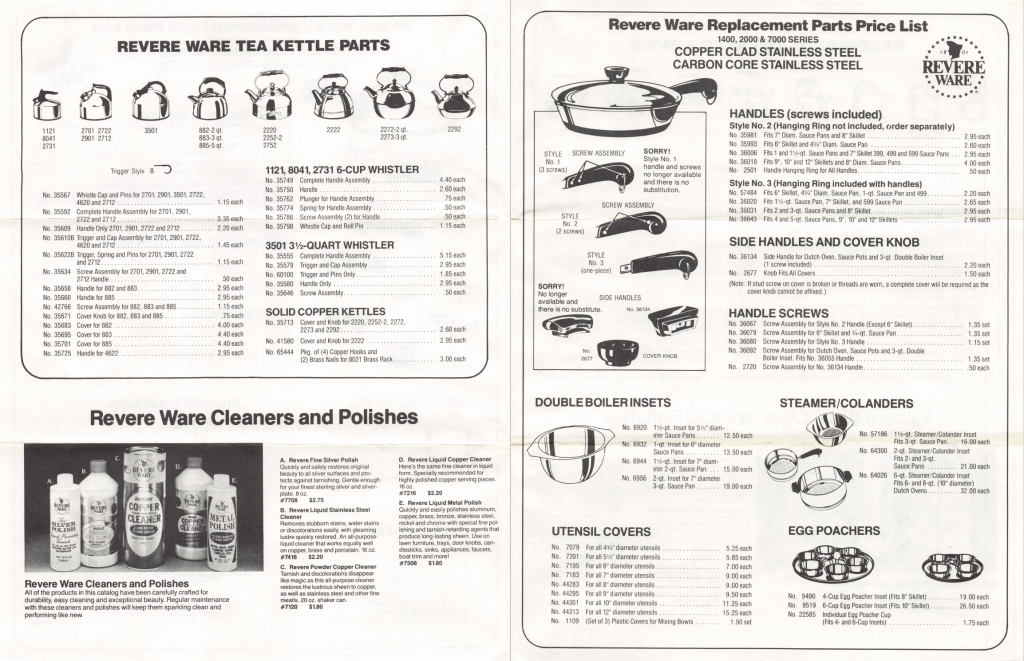
Quite a bit fewer parts. But at that point, you were lucky to get anything, because, a year or two later, they stopped selling any replacement parts.
The problem started in the 1960’s when other cookware types started coming out and stealing the thunder from Revere Ware, which up until that point had pretty much been king of the castle. As their sales fell, they looked to broaden their offering to align with what people were looking for, and to reduce costs. It was at that point, in 1968 that they redesigned their iconic copper bottom cookware to use about half the metal, and with a much simpler one piece Bakelite handle design. It helped, but Revere Ware still struggled financially.
In 1982, unfortunately, Revere filed for bankruptcy, mainly due to losses in their aluminum division; while the cookware division did remain profitable, it wasn’t enough. This is presumably when the bean counters really got to work and looked for every opportunity to slash costs. From this point on, Revere was never again about making good products (they hadn’t been since the late 60s) or serving the customers well. They submitted to a takeover in 1996, and the new owners (World Kitchen) went through another bankruptcy in 2002. During these periods and beyond, they were really just trying to wring profits on the back of the brand history, and running the business as cheaply as possible.
Truth be told, the stuff produced from the 90’s through the discontinuation of the brand in 2018 ranged from poor to bad. They would sort of support warranty claims then (they still claimed to have a 25 year warranty), but didn’t have a whole lot of selection to send you in replacement, especially in the latter part of those three decades.
In the mid-2000’s, my wife and I loved thrifting; we didn’t have kids at that point. Among the things we picked up were some Revere Ware pans; I felt a little nostalgic about them, recalling my mother had some in the 60’s and 70’s. But, the handles were in poor shape so I set out to see if I could find replacement online. No such luck. What I did find was the occasional new-old-stock replacement on eBay, and, a guy named Charlie Anjard, who ran the Shine Shop. He took old Revere Ware and refurbished it. He cleaned the metal of the pans and then polished them using industrial processes. The Bakelite, he subjected to sanding with progressively finer and finer sand paper to remove the damaged Bakelite and expose the undamaged part. Everything came out looking like new.
Here is a bunch I had done by the person that took over from Charlie. The Bakelite, of course, is ours.
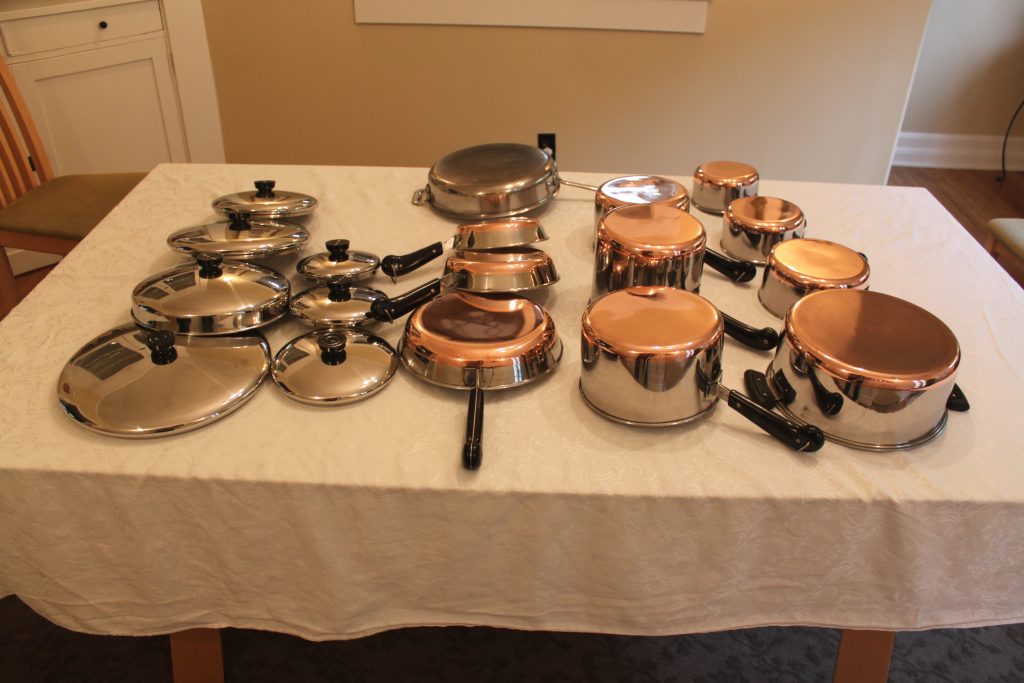
Charlie also put together the Revere Ware history and photo guide pages, and collected a lot of information on the history of Revere Ware, which got me even more interested in the brand.
It was at that point I thought I’d see how hard it would be to have some replacement parts manufactured; I have another business that is also involved in manufacturing, so this wasn’t too much of a stretch. I turned out to be doable and I’ve slowly expanded my offerings since 2009.
Granted, what we offer now is a fraction of what Revere Ware offered in the day. But unfortunately, as a small shoestring operation, we have to keep profitability in mind. There are two big obstacles in having parts manufactured – the cost of molds, and minimum order quantities. A mold can cost several thousand dollars. That means if we say, make 30% in the end on $10 parts that come from a mold that costs $3,000, we have to think we can sell 1,000 of them just to break even on the cost of the mold. Often times, a contract manufacturer requires that you purchase a minimum of 5,000 or so parts, which sets the bar even higher. We have to think we can sell that many in 3-5 years for it to make sense.
I think the range of parts we currently sell covers perhaps 70% of what people are looking for these days. One way to provide more would be to build 3D models of the parts that can then be printed in an appropriate materials using 3D printing services. We did exactly that for the trigger for the 3 1/2 quart kettle.
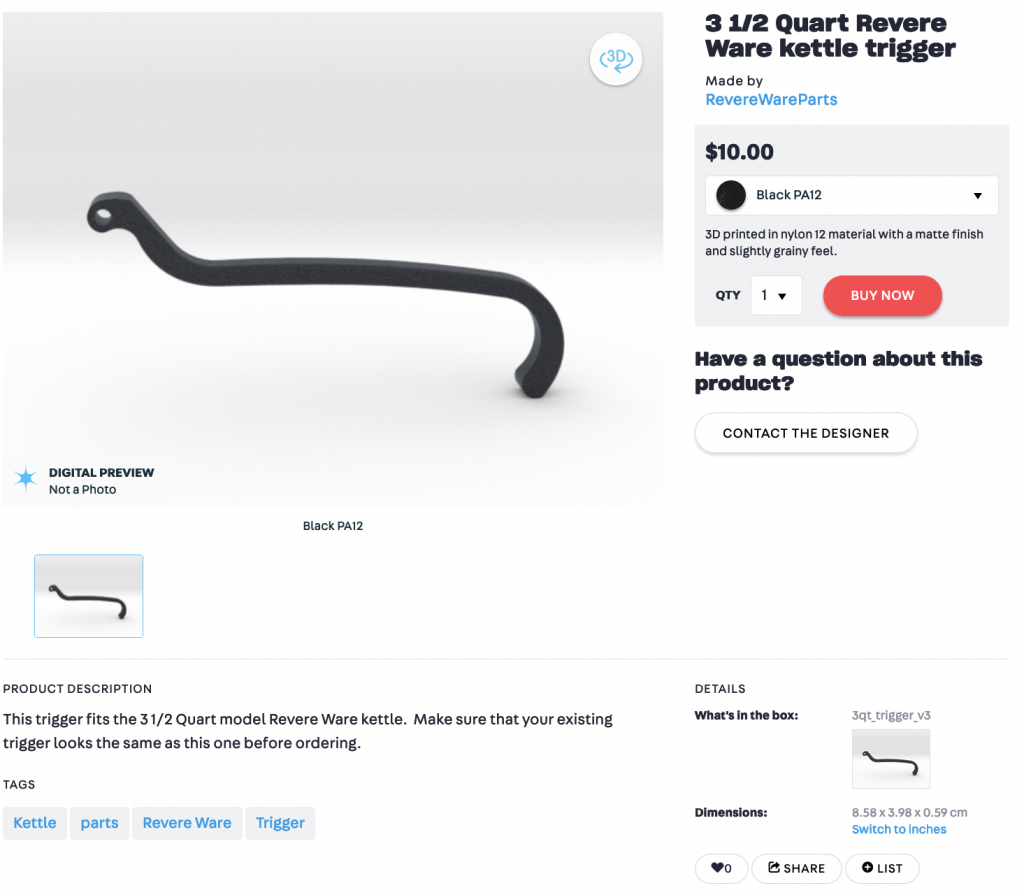
3D printed parts aren’t cheap; that one will set you back over $22 in the end, and that’s without us marking up the cost at all.
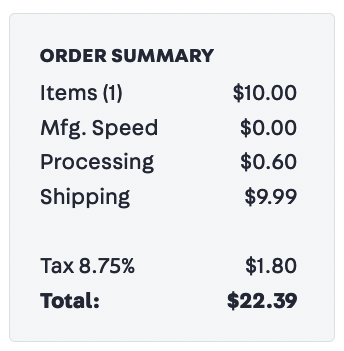
To date, we’ve sold 87 of that trigger through Shapeways. You can probably see what I am getting at here; if we had spent the money to make those triggers, incurred the cost of a mold, and ordered 5,000 of them, we would have lost money.
So, 3D printed parts aren’t cheap, but they are better than no part at all, if you want to keep your cookware for nostalgic reasons. I would love to develop more 3D models for parts, but there are a couple of problems. First, I am not a mechanical engineer; I managed to make the model of the trigger through a lot of trial and error, and it was a bit of a struggle. Second, there aren’t yet materials for every use (but presumably some day there will be).
On the bright side, 3D printing can also help prove if demand is there or not. If orders for 3D printed parts prove there is enough demand, having a 3D model makes a part that much easier to manufacture.
Revere Ware enthusiasts might be loosely called a community, of sorts. I’d love it if any members of this community of are mechanical engineers would offer to design some replacement part models for the things people are looking for. I’d be happy to host a library of these here. Some food for thought.